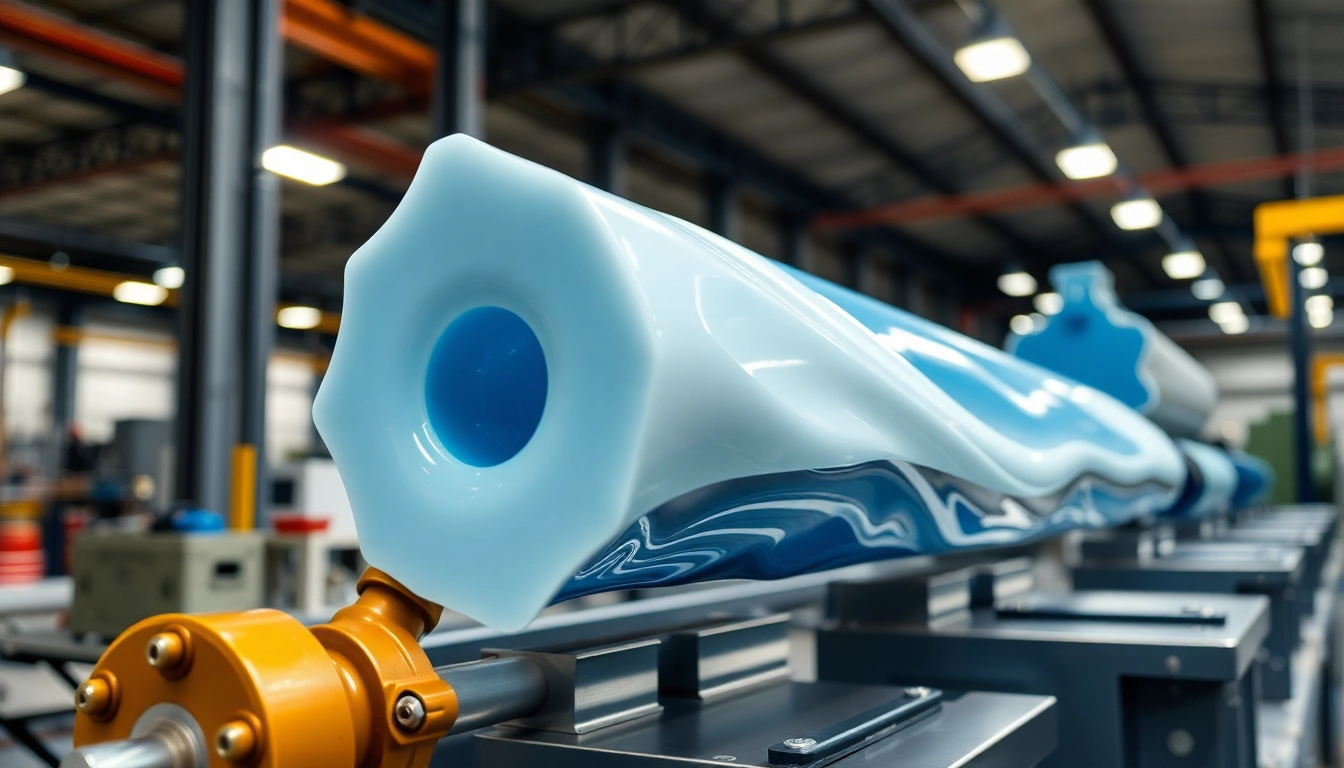
Understanding Blow Molding Technologies
What is Blow Molding?
Blow molding is a manufacturing process used primarily for creating hollow plastic parts. This technique is highly efficient for producing containers, automotive components, and various other items in substantial volumes. The process involves melting plastic and forming it into a pre-formed shape known as a parison, which is then inflated inside a mold to achieve the desired final shape. The versatility and efficiency of blow molding make it an essential process in the modern manufacturing landscape.
Types of Blow Molding Processes
There are three primary types of blow molding processes: extrusion blow molding, injection blow molding, and stretch blow molding. Each type has its unique applications and benefits:
- Extrusion Blow Molding (EBM): In this method, plastic is extruded into a tube or parison, which is then clamped into a mold. Air is blown into the parison, expanding it to fit the mold’s shape. EBM is best suited for producing items like bottles and containers and is known for its efficiency and cost-effectiveness.
- Injection Blow Molding (IBM): This process combines injection molding and blow molding. A preform is produced by injection molding, and then it is placed in a blow mold where air is blown to form the final product. IBM is particularly advantageous when producing small, precision components that require closer tolerances.
- Stretch Blow Molding (SBM): Stretch blow molding is a specialized process where the preform is heated and stretched both longitudinally and radially before being blown into shape. This method is ideal for producing stronger and lighter bottles, typically used in the beverage industry, resulting in enhanced clarity and strength.
Applications of Blow Molding in Various Industries
Blow molding processes are widely utilized across several industries, including:
- Food and Beverage: The production of bottles and containers for beverages, sauces, and other food products.
- Personal Care: Packaging for shampoos, lotions, and health care products.
- Pharmaceuticals: Bottles and containers that require precise dosing and compliance with stringent safety regulations.
- Automotive: Components such as fuel tanks, dashboard elements, and various exterior parts.
- Consumer Goods: Toys, tools, and various household products.
Choosing the Right Blow Molding Machine Supplier
Key Factors in Supplier Selection
Finding an appropriate Blow Molding Machine Supplier involves careful consideration of various factors. Key elements to evaluate include:
- Experience and Expertise: Assess the supplier’s experience within the blow molding industry and their knowledge of the specific technologies relevant to your needs.
- Product Range: A supplier should offer a wide range of blow molding machines and technologies to cater to different production requirements.
- Customization Capabilities: Evaluate if the supplier provides custom solutions based on your specific production needs and volume requirements.
- Customer Reviews and References: Research customer feedback and case studies on the supplier’s previous projects.
Evaluating Supplier Capabilities and Technologies
It’s crucial to assess the supplier’s capacity to meet your production demands. This evaluation should cover:
- Machine Specifications: Verify if the machines’ specifications align with your operational needs, including the production capacity, cycle times, and energy consumption.
- Innovative Technologies: Look for suppliers that incorporate the latest technology in their machines, such as energy-efficient systems, advanced controls, and automation capabilities.
- Testing and Quality Assurance: Inquire about the testing procedures for machines before delivery and the quality assurance measures in place to ensure reliability and performance.
Understanding Supplier Warranties and Support
Understanding the warranty and post-purchase support is vital for the longevity and performance of the machinery. Consider the following aspects:
- Warranty Coverage: Examine the terms and length of the warranty. Ensure it covers future maintenance and protection against defects.
- Technical Support: Verify the availability of technical support after installation. Determine if the supplier offers remote assistance and on-site service if required.
- Spare Parts Availability: Ensure that the supplier provides readily available spare parts, along with a clear process for ordering them.
Cost Considerations When Buying Blow Molding Machines
Initial Investment vs. Long-term Savings
When acquiring blow molding machines, assessing the initial investment against long-term operational savings is essential. While high-quality machines may have higher upfront costs, they often lead to lower operational costs due to:
- Energy Efficiency: Advanced machines are designed for energy efficiency, which can significantly reduce production costs over time.
- Reduced Material Waste: Machines equipped with enhanced technologies minimize material waste.
- Higher Throughput: Investing in faster machines can lead to a higher output, thus enhancing profitability.
Understanding Different Pricing Structures
Different suppliers may have varying pricing structures based on several factors:
- Type of Machine: The specific technology utilized (EBM, IBM, SBM) will influence prices. Typically, injection and stretch blow molding machines can be more expensive due to their complexity.
- Machine Size and Capacity: Larger machines capable of higher production rates usually come with a higher price tag.
- Customization Options: Customized machines tailored for specific production needs may result in higher costs due to additional features and specifications.
Calculating Return on Investment (ROI)
To determine the ROI for your blow molding machine purchase, you should consider:
- Payback Period: Calculate how long it will take for savings generated from the machine to cover its cost.
- Operational Costs: Factor in maintenance, labor, and material costs in your analysis to get a clear picture of ongoing expenses.
- Profit Margins: Assess how much your products’ profit margins can improve with the new machine.
Maintaining Your Blow Molding Equipment
Regular Maintenance Practices
Regular maintenance practices are fundamental to ensuring the longevity and efficiency of blow molding equipment. These include:
- Scheduled Inspections: Conduct routine inspections of critical components, checking for wear and tear.
- Lubrication: Regularly lubricate moving parts to reduce friction and prevent premature wear.
- Cleaning: Ensure that the molds are cleaned regularly to prevent contamination and defects in the finished products.
Troubleshooting Common Issues
Common issues that may arise with blow molding machines can be addressed with prompt troubleshooting:
- Unstable Product Dimensions: Check mold alignment and air pressure; recalibrate if necessary.
- Surface Defects: Inspect for material consistency, temperature settings, and cooling rates.
- Machine Downtime: Implement a preventive maintenance program to reduce unexpected downtimes due to mechanical failures.
When to Contact Your Supplier for Support
Recognizing when to contact your supplier is vital to maintaining optimal machine performance. Consider reaching out when:
- You’re unable to resolve an issue after standard troubleshooting procedures.
- There are frequent breakdowns or system errors beyond your technical ability to fix.
- You need specialized training for optimal use or programming of new machinery features.
Future Trends in Blow Molding Technology
Advancements in Machine Efficiency
The future of blow molding technology is likely to focus significantly on machine efficiency. Emerging trends include:
- Digitalization: The integration of IoT (Internet of Things) for real-time monitoring and predictive maintenance capabilities.
- Automation: Utilizing robotics and automation in production processes to increase speed and precision.
- Energy Optimization: Future machines will be designed to consume less energy, reducing operational costs and environmental impact.
Eco-friendly Innovations in Blow Molding
The push towards sustainability is driving innovations in blow molding. Key developments are:
- Biodegradable Materials: Developing machines that can work with bioplastics that break down more easily and do not contribute to environmental pollution.
- Recycling Capabilities: Enhancing machines to efficiently process recycled materials, thereby reducing waste.
- Energy Recovery Systems: Integrating systems to recover energy from the manufacturing process, promoting a circular economy model.
Shifts in Market Demand and Consumer Preferences
As industries evolve, so do market demands and consumer preferences, impacting blow molding technology:
- Customization: An increasing preference for customized products is pushing suppliers to offer flexible manufacturing solutions.
- Higher Quality Standards: Consumers demand higher quality products, driving innovation in processing technologies
- Sustainability Expectations: Growing awareness of environmental issues is leading companies to prioritize sustainable practices and products.