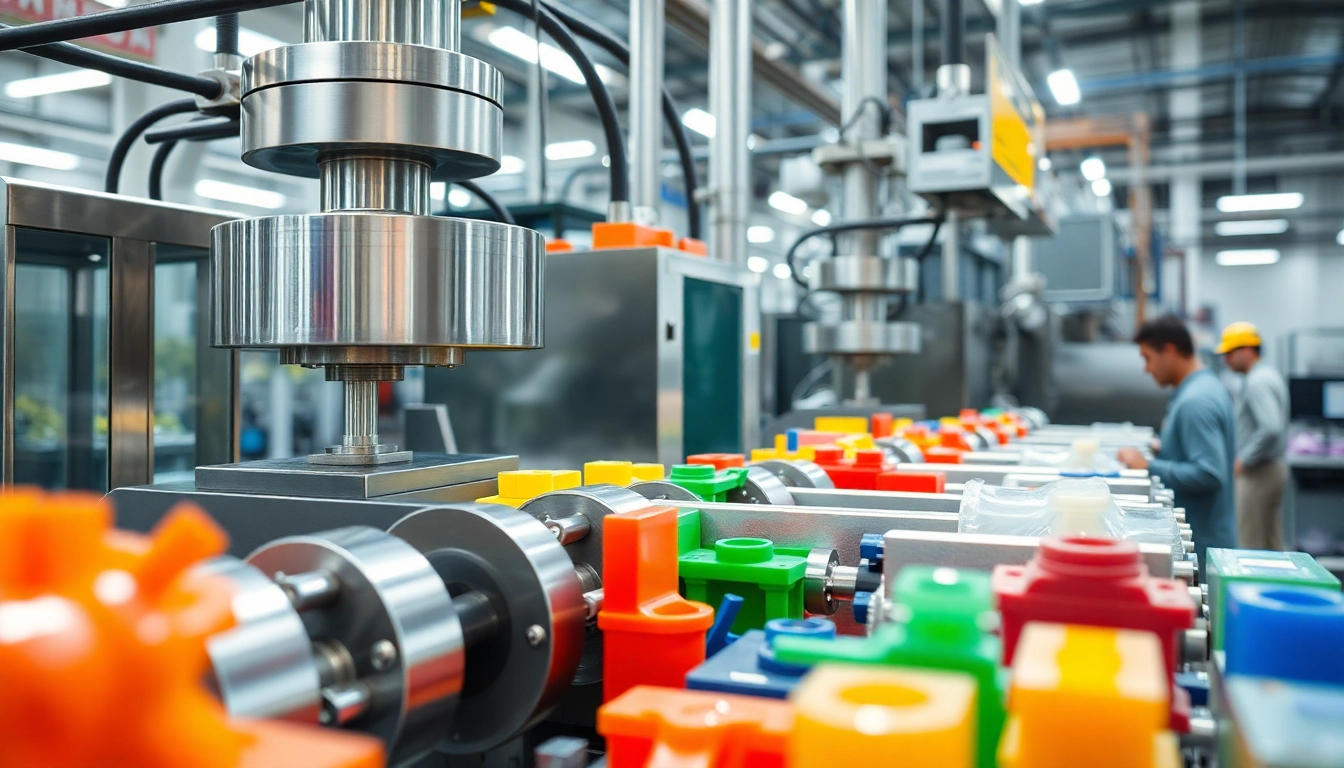
Understanding Blow Molding Technology
What is Blow Molding?
Blow molding is a manufacturing process widely used for producing hollow plastic parts. This technique is essential in creating items such as bottles, containers, and various plastic parts. It involves forming a plastic tube, known as a parison, which is heated and then air is blown into it until it takes the shape of a mold. The resulting products are lightweight, durable, and can be made in various shapes and sizes, making blow molding a key process in the packaging and automotive industries.
Types of Blow Molding Processes
There are three primary variations of blow molding processes:
- Extrusion Blow Molding: This is the most common form, where plastic is melted and extruded into a parison. The parison is then clamped in a mold, and air is introduced to expand it into the desired shape.
- Injection Blow Molding: In this method, a preform is first created through injection molding, then it is subsequently blown into the final shape. This process is often used for small, precise containers.
- Stretch Blow Molding: This technique involves stretching the parison both axially and radially. This process is particularly utilized for producing bottles with enhanced structural integrity and clarity, often seen in the beverage industry.
Applications in Various Industries
Blow molding technology finds applications across a multitude of industries:
- Packaging: The most notable application of blow molding is in packaging, especially for beverages, cleaning products, and personal care items.
- Automotive: Components such as fuel tanks and air ducts are commonly produced using blow molding due to their lightweight and durable characteristics.
- Consumer Goods: Items like toys, household products, and sporting goods are often made through blow molding, allowing for diverse shapes and sizes.
- Medical Devices: Certain medical containers are produced using blow molding, ensuring safety and sterility in healthcare applications.
The Role of a Reliable Blow Molding Machine Supplier
Benefits of Choosing Experienced Suppliers
Choosing the right blow molding machine supplier can significantly impact your manufacturing efficiency and output quality. An experienced supplier brings not only their industry expertise but also a network of support and innovation. They often offer tailored solutions that align with specific production needs and can guide businesses through complex decision-making processes related to machinery selection.
Quality Assurance and Machine Specifications
A reputable supplier ensures that their machines meet high-quality standards and comply with industry regulations. They provide detailed technical specifications and demonstrate the capabilities of their machines through comprehensive documentation and trials. Furthermore, high-quality machines often mean lower defect rates and improved product quality, which can lead to long-term savings and reduced waste.
Customer Support and After-sales Service
A vital aspect of choosing a blow molding machine supplier is their customer support and after-sales service. Reliable suppliers offer comprehensive training for staff on machine operation, as well as ongoing technical support to troubleshoot issues that may arise during production. Excellent after-sales service can help minimize downtime and maintain production efficiency.
Key Features to Look for in Blow Molding Machines
Energy Efficiency and Sustainability
With growing emphasis on sustainability, energy-efficient blow molding machines are more important than ever. These machines are designed to consume less energy while maintaining high productivity levels, making them cost-effective and environmentally friendly. Features such as variable frequency drives (VFDs) can help optimize power usage without sacrificing performance.
Automation and Technology Integration
Modern blow molding machines increasingly incorporate automation and advanced technology. Automated systems can enhance precision in production, reduce labor costs, and increase overall efficiency. Features such as real-time monitoring systems can track machine performance and maintenance needs, ensuring that any potential issues are addressed proactively.
Customizability for Specific Production Needs
Not all production needs are created equal; hence, flexibility in machinery is crucial. A quality blow molding machine supplier will offer customizable solutions that can be adapted to different production requirements, from modifying mold sizes to adjusting production speeds. This adaptability ensures that businesses can remain competitive in a rapidly evolving market.
Cost Factors When Sourcing Blow Molding Machines
Initial Investment vs. Long-term Savings
Investing in blow molding machines involves significant initial costs, but it’s essential to consider the long-term savings. A robust, well-engineered machine will often yield lower operational costs over time, owing to factors such as durability, reduced maintenance needs, and energy efficiency. Businesses should conduct a total cost of ownership analysis to understand how upfront expenses can translate into future savings.
Maintenance Costs and Durability
The durability of a blow molding machine directly impacts maintenance costs. Machines that require frequent parts replacement or repairs can erode profit margins significantly. It is advisable to review the warranty terms and the availability of spare parts when selecting a machine. Regular maintenance checks and adhering to scheduled servicing can prolong a machine’s life and improve its performance.
Financing Options for Businesses
Understanding available financing options can ease the burden of upfront costs associated with purchasing blow molding machines. Many suppliers offer financing programs, leasing options, or payment plans that can help businesses manage cash flow effectively while still investing in crucial technology. Additionally, examining grants or financial aid for manufacturing technology investment may provide further financial relief.
Future Trends in Blow Molding Technology
Innovations Driving the Industry Forward
The blow molding industry is evolving rapidly, with technological innovations paving the way for enhanced productivity and product quality. Emerging technologies such as AI and IoT are being integrated into manufacturing processes, allowing for better data analytics, predictive maintenance, and enhanced decision-making capabilities.
Sustainability Trends and Eco-friendly Alternatives
As environmental concerns continue to rise, the industry is witnessing a significant shift towards sustainable practices. This includes using recycled materials, biodegradable plastics, and designing products that can be easily reused or recycled. Machine manufacturers are also focusing on creating processes that minimize waste and reduce energy consumption, aligning with global sustainability goals.
Emerging Markets and Global Demand Insights
Global demand for blow molding technologies is on the rise, particularly in developing markets. As industries such as packaging, automotive, and consumer goods grow in these regions, suppliers must consider local needs, regulatory landscapes, and market conditions. Businesses that anticipate these trends can position themselves advantageously and cater to an expanding audience.
In conclusion, sourcing a blow molding machine from a credible Blow Molding Machine Supplier is critical for the efficiency and effectiveness of your manufacturing processes. By understanding the technology, considering the critical factors discussed, and keeping an eye on future trends, your business can make informed decisions that lead to success in a competitive landscape.