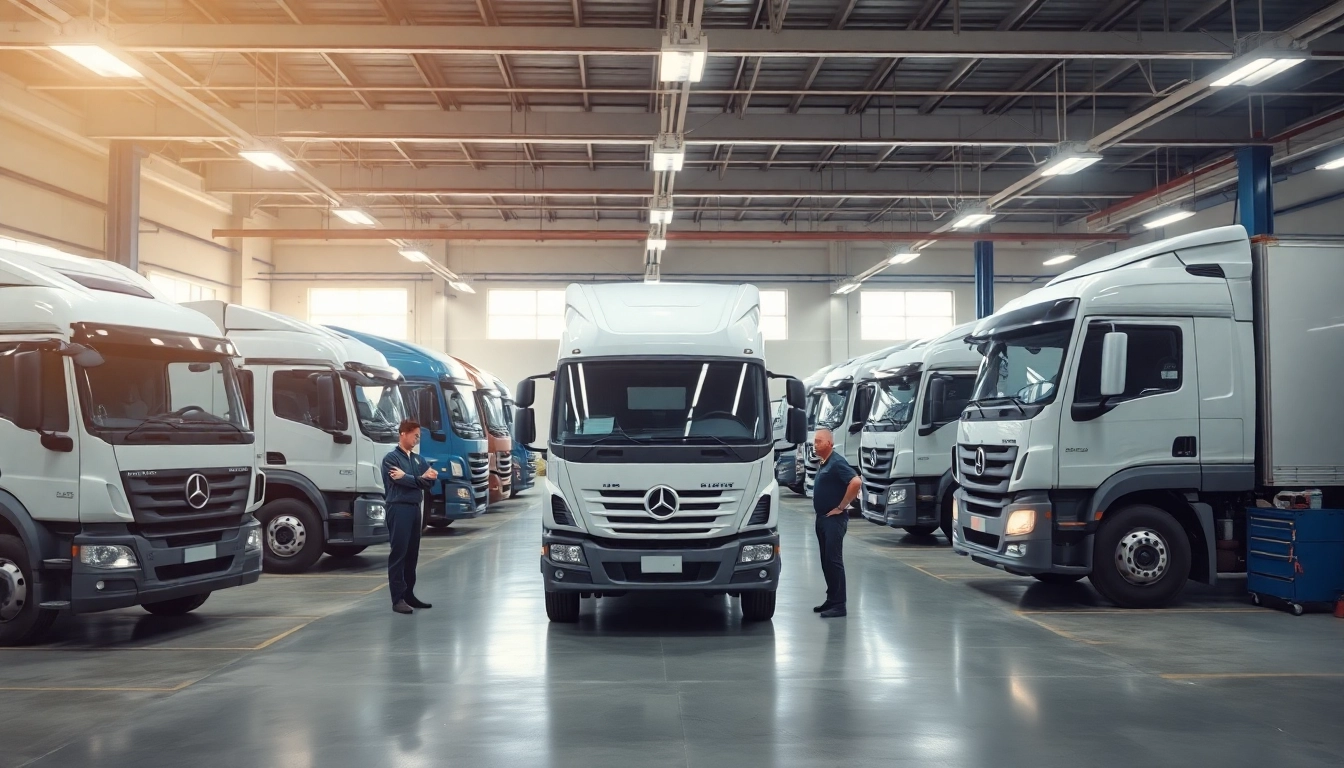
Understanding Preventive Maintenance for Fleets
What Is Preventive Maintenance?
Preventive maintenance (PM) refers to the routine maintenance activities that fleet managers undertake to minimize the risk of equipment failure and extend the life of their vehicles. This proactive maintenance approach helps ensure that fleet vehicles are well-maintained and in optimal working condition. The goal is to anticipate maintenance needs before they escalate into significant repairs or position the vehicle out of service.
Implementing a robust preventive maintenance for fleets strategy involves regular inspections, servicing, and parts replacements based on established schedules rather than waiting for components to break down. This method fosters a culture of safety and reliability in fleet operations.
Importance of Preventive Maintenance for Fleets
Preventive maintenance is crucial for several reasons:
- Increased Uptime: By addressing potential issues early, fleets can reduce the chances of unexpected breakdowns, leading to improved vehicle availability.
- Cost Reduction: Preventive maintenance helps avoid expensive repairs stemming from neglect, thus lowering overall fleet operating costs.
- Enhanced Safety: Regular inspections and maintenance ensure that vehicles meet safety standards, reducing the likelihood of accidents and saving lives.
- Extended Vehicle Life: Maintaining vehicles properly helps extend their lifespan, maximizing return on investment (ROI).
Common Myths About Fleet Maintenance
Many misconceptions about preventive maintenance can hinder effective fleet management. Here are a few common myths:
- Myth 1: “Preventive maintenance is an unnecessary expense.” Many businesses view PM as an added cost; however, it is an investment that can save substantial amounts of money over time.
- Myth 2: “Maintenance can wait until something breaks.” Waiting for a failure can lead to greater costs and downtime than conducting regular preventive measures.
- Myth 3: “All maintenance tasks are the same.” Different vehicles require different maintenance strategies. A “one-size-fits-all” approach doesn’t work in fleet management.
Key Components of a Fleet Maintenance Program
Creating a Comprehensive Maintenance Schedule
A successful fleet maintenance program begins with a comprehensive maintenance schedule. It should include:
- Regular oil and filter changes
- Tire rotations and replacements
- Brake inspections, including pads and rotors
- Fluids checks, including transmission and coolant
- Battery inspections
Each vehicle may require a unique schedule based on its usage patterns, mileage, and manufacturer recommendations. For example, high-use vehicles might require more frequent checks than those used less aggressively.
Essential Tools and Technologies for Fleet Maintenance
Modern fleet maintenance incorporates various tools and technologies to streamline processes and enhance efficiency. Some essential tools include:
- Fleet Management Software: These platforms can automate scheduling, tracking service histories, and managing parts inventories.
- Telematics: Utilizing GPS and sensor data to monitor vehicle performance and identify potential maintenance needs in real-time.
- Mobile Apps: Allowing technicians to access maintenance schedules and perform inspections on-the-go, increasing responsiveness and efficiency.
Common Types of Preventive Maintenance Tasks
Fleet management teams should regularly conduct several types of preventive maintenance tasks, including:
- Fluid changes (engine oil, brake fluid, transmission fluid)
- Tire maintenance (inflation checks, rotations, and alignments)
- Brake inspections (checking the condition of pads, discs, and fluid)
- Battery checks (inspecting terminals and the charge level)
- Wiper blade replacements (ensuring visibility during adverse weather)
Establishing a routine for these tasks helps create accountability and promotes a culture of safety and efficiency.
Best Practices to Implement a Maintenance Program
Steps to Develop an Effective Fleet Maintenance Plan
To create an effective fleet maintenance plan, consider these steps:
- Assess Current Practices: Analyze current maintenance schedules, costs, and vehicle performance to identify areas requiring improvement.
- Set Clear Goals: Establish measurable objectives for uptime, safety compliance, and cost savings.
- Create Checklists: Develop detailed checklists outlining required maintenance tasks, inspection points, and schedules for each vehicle.
- Allocate Resources: Assign budget, personnel, and tools required to achieve your maintenance goals.
- Implement Technology: Leverage appropriate fleet management software and telematics to monitor fleet health in real-time.
Training and Involving Your Fleet Team
Staff training is integral to a successful preventive maintenance program. Ensure your team understands the importance of preventive maintenance and how to execute it effectively. Key training elements may include:
- Understanding vehicle systems and their maintenance needs
- Operating and using fleet management software
- Safety protocols during inspections and maintenance activities
- Recognizing potential issues before they become major problems
Involving your team in the maintenance process empowers them, creates accountability, and fosters a proactive maintenance culture.
Utilizing Software for Maintenance Tracking
Tracking maintenance activities via software is vital for maintaining an organized fleet operation. Use digital solutions that offer:
- Automated alerts for upcoming maintenance tasks based on usage and interval settings
- Data analysis tools to interpret maintenance history and performance metrics
- Integration with telematics to provide real-time data insights
These features enhance visibility into fleet performance and encourage timely interventions when issues arise.
Monitoring and Evaluating Fleet Performance
Key Performance Indicators for Fleet Maintenance
To evaluate the effectiveness of preventive maintenance efforts, it is essential to track key performance indicators (KPIs), including:
- Maintenance Cost per Vehicle: Track total costs associated with maintenance for each vehicle in the fleet.
- Vehicle Uptime Percentage: Measure the percentage of time vehicles are operational versus out of service.
- Number of Accidents or Incidents: Monitor safety-related incidents to assess the effectiveness of maintenance protocols.
- Average Fleet Age: Analyze the age of the fleet to determine if replacement strategies are needed.
Continuous Improvement through Data Analysis
Regularly analyze maintenance data to identify trends and patterns that can inform future maintenance strategies. Key aspects to analyze include:
- Recurring issues across different vehicles or types
- Seasonal trends that affect vehicle performance
- Maintenance costs correlated with vehicle age or mileage
By evaluating these trends, fleet managers can adjust their strategies to improve both cost-effectiveness and vehicle reliability.
Adjusting Maintenance Schedules Based on Feedback
Feedback from maintenance staff and drivers should be collected to refine the maintenance schedule continually. This feedback is crucial for identifying:
- Tasks that require more frequent attention due to wear and tear
- Processes that may be streamlined for efficiency
- Adjustments needed to address new challenges or evolving fleet needs
Frequent revisits to the maintenance schedules based on real-time data and feedback can significantly enhance the fleet’s operational reliability.
The Future of Preventive Maintenance in Fleet Management
Emerging Technologies and Trends in Fleet Maintenance
The future of preventive maintenance is closely tied to advancing technologies. Key trends include:
- Artificial Intelligence (AI): Utilizing AI to predict equipment failures before they occur based on historical data analysis.
- Predictive Maintenance: Shifting focus from scheduled maintenance to condition-based maintenance, where interventions are made based on actual vehicle conditions.
- Electric and Autonomous Vehicles: As fleets become more electrified and automated, maintenance strategies will need to adapt to new technology and components.
Integrating Sustainability Practices in Fleet Management
As sustainability becomes a paramount concern, fleet maintenance programs are evolving to include more environmentally responsible practices. Key strategies involve:
- Utilizing sustainable materials in repairs and replacements
- Implementing recycling programs for used parts and fluids
- Adopting alternative fuels and electric vehicles to reduce carbon footprints
These practices not only benefit the environment but can also result in cost savings in terms of fuel consumption and regulatory compliance.
Preparing for Future Challenges in Fleet Maintenance
The landscape of fleet management is constantly changing, with challenges such as increasing regulations, rising costs, and technological obsolescence. Fleet managers must:
- Stay informed about industry developments and regulatory changes
- Invest in ongoing training for staff to keep abreast of new technologies
- Be flexible and ready to adjust procedures based on emerging challenges and opportunities.